Design of new laundry to be built in the Middle East
The Challenge
WSP has been asked to design a new laundry with a capacity of 130 tonnes per day, which will wash items from hotels with a total of more than 8,000 rooms. The laundry is part of a large project in the Middle East.
Before designing a new laundry, it is advisable to carry out an engineering assignment to establish a list of requirements. During the engineering assignment, the focus is mainly on internal logistics, where efficient operations will lead to high productivity. Financial and energy issues are also considered.
Detailed information is required for comprehensive advice and design. While some WSP questions might have seemed unusually detailed, they contribute to positive outcomes by providing accurate advice.
- Request for detailed advice on a new laundry design ready for tendering
- Laundry service for 8,000 hotel rooms and hotel employees
- Laundry capacity of 130 tonnes per day
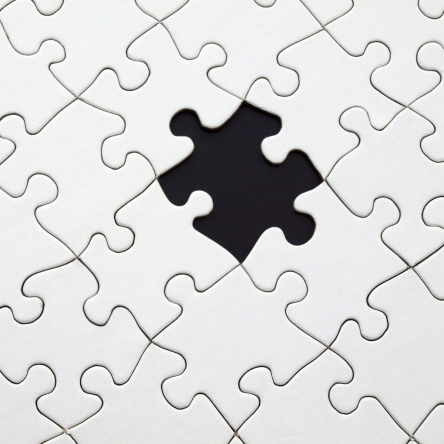
The Solution
To get started quickly, a preliminary layout of the laundry was sketched before the final engineering contract was awarded. This built confidence and led to the final design and engineering contract. The design of the new laundry was developed in collaboration with construction, energy management as well as facilities engineering partners.
The project is structured as a Stage Gate Process, a project management technique with multiple stages and decision points to proceed to the next step.
After approval of the layout and further steps, full engineering of the project was commissioned using Building Information Modelling (BIM). The BIM model provides a three-dimensional view of all elements, including quantities, materials and finishes. Information that can be used in the tendering process.
- Laundry layout
- Stage Gate process
- BIM model
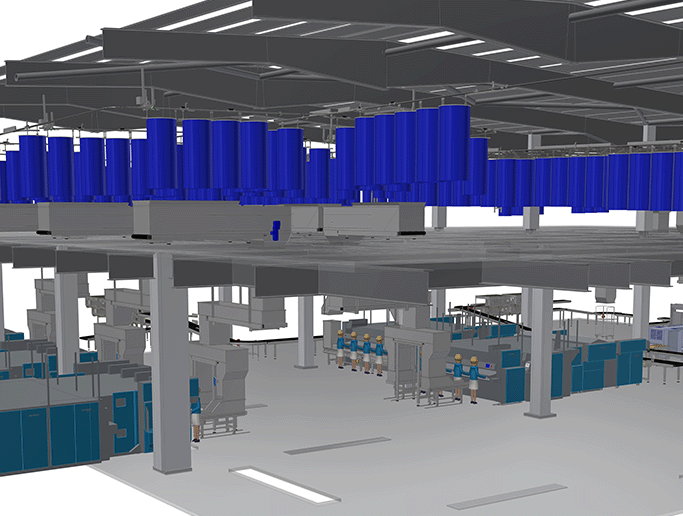
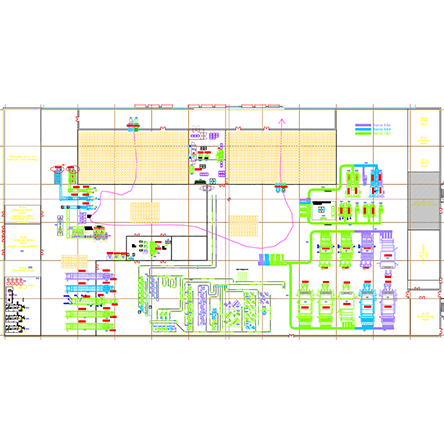
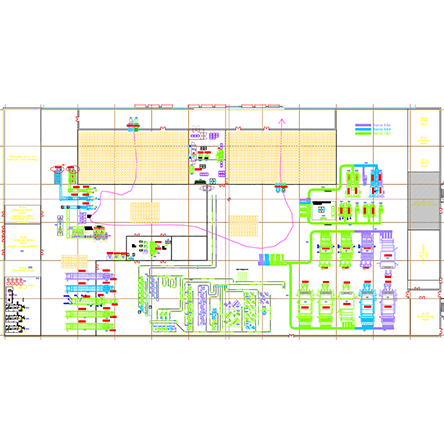
Detailed WSP questions lead to accurate advice and positive outcomes.
3D design
The Result
The engineering process for the new laundry resulted in a comprehensive Request for Proposal (RFP) that clearly articulated sustainability and logistics requirements. The result is a fully RFID-based logistics process and an exceptionally high level of quality for linen, towels and workwear.
The detailed engineering as well as the laundry specific requirements served as the basis for the customer’s equipment tender, in which WSP played an advisory role. As a system integrator, WSP Systems has a coordinating role in the overall control of the laundry with the WinWash2 control and all internal logistic flows.
- Design based on RFID process
- Design for high-quality
- Design for high-productivity laundry
- Design for a sustainable and efficient laundry
- Information for the right investments
- Ready for tendering